Sugar Beet Pulp Dryer
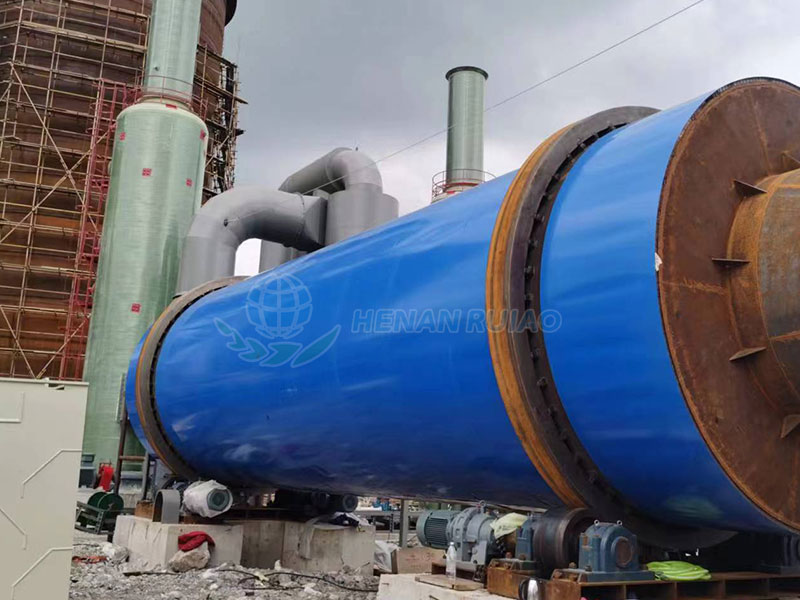
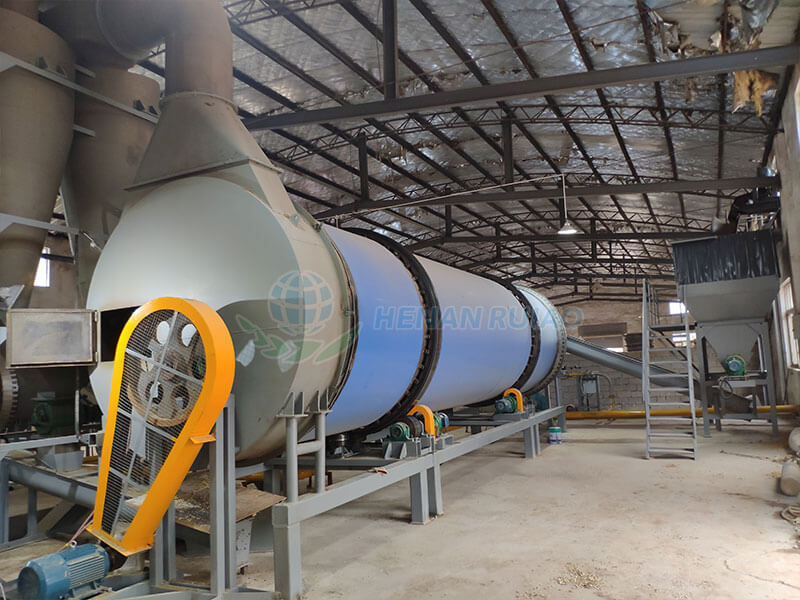
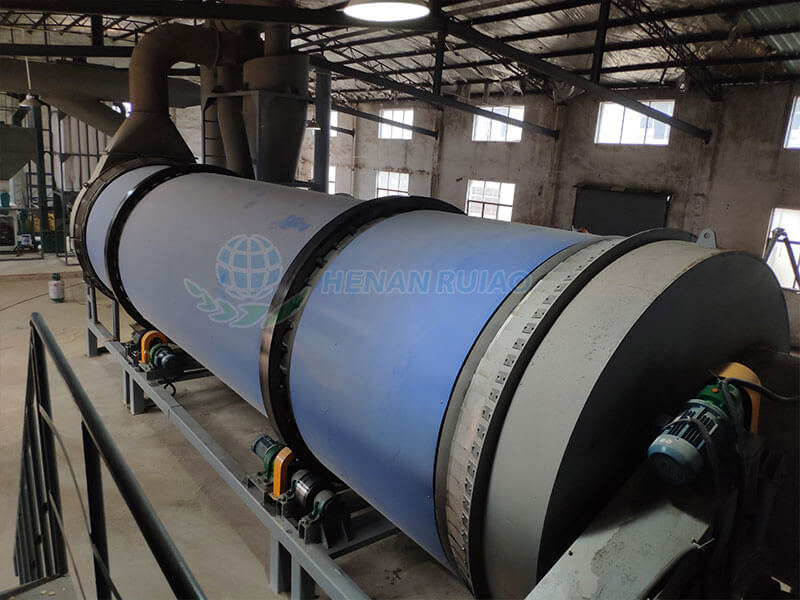
Introduction
The sugar beet residue has high moisture content, high sugar content, and easy adhesion. Henan Ruiao adopts unique technologies and processes to solve the technical difficulties in the drying process of sugar beet residue. It is suitable for drying various fruit residues such as apple residue, pineapple residue, and citrus residue. The entire drying system consists of coal-fired hot blast stove, feeding and discharging equipment, rotary drum dryer, dust removal system, electrical control system, high and low temperature pipelines and other mechanisms.
Advantages
1. Equipped with special dispersing device, the processed material is relatively loose and the viscosity is greatly reduced, solving the problem of wall sticking during the drying process.
2. The combination drying process solves the problem of easy saccharification and gelatinization during the drying process of sugar beet residue, achiving higher utilization rate of heat energy.
3. The operating parameters can be adjusted according to the properties of different materials, so that the materials can form a stable material curtain inside the dryer cylinder, and the mass and heat exchange is more sufficient.
4. The entire drying system adopts electrical centralized control, with a high degree of automation and convenient operation.
5. After the drying section, it can be connected to subsequent sections such as crushing, mixing, granulation, and packaging to produce sugar beet feed pellet feeds.
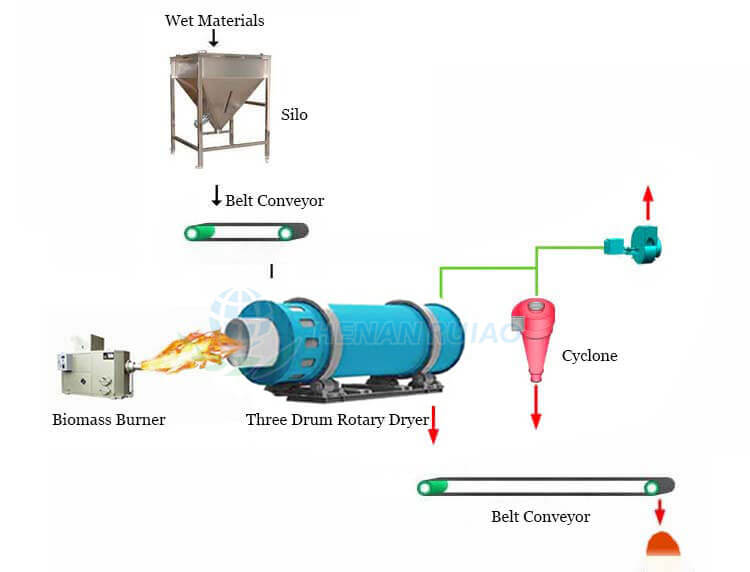
Application
The sugar beet pulp drying production line is applicable for drying of high-moisture materials with 50%-85% moisture, such as sugar beet pulp, sugarcane bagasse, sludge, bean dregs, starch residue, and sauce residue, spray corn bran, olive oil pomace,cassava dregs, brewer’s grains, distiller’s grains, straw, grass, organic fertilizer, chicken beef feces. We also help optimize the drying process according to the property of different materials, production scale, application requirements, cost control, automation level, and site condition.
Working Principle
After removing some water from the sugar beet residue through a screw dehydrator, it is transported by a screw conveyor to the sugar beet residue dryer. Under the flipping of uniformly distributed lifting boards in the cylinder, it fully contacts with hot air, achieving the purpose of heat and mass transfer. The dried sugar beet residue has good color, low nutritional loss, strong palatability, and is loved by animals.
Technical Parameters
Model | RASG2010-3 | RASG2209-3 | RASG2609-3 | RASG3009-3 |
Capacity | 1-2t/h | 1-2t/h | 2-3t/h | 4-6t/h |
Input moisture | 35-60% | |||
Output moisture | 12-15% | |||
Drying temperature | 450℃ | |||
Floor space | 10m×20m | 10m×20m | 15m×30m | 15m×40m |
Send a Message
Get In Touch!
Address
No.11 Changchun Road, High-Tech Development Zone, Zhengzhou, Henan, China
- 19900970386