Lignite Dryer
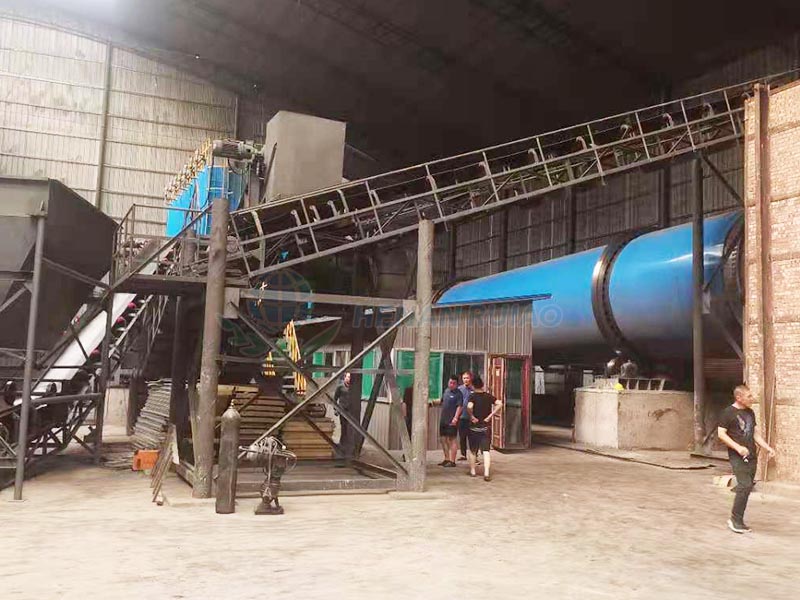
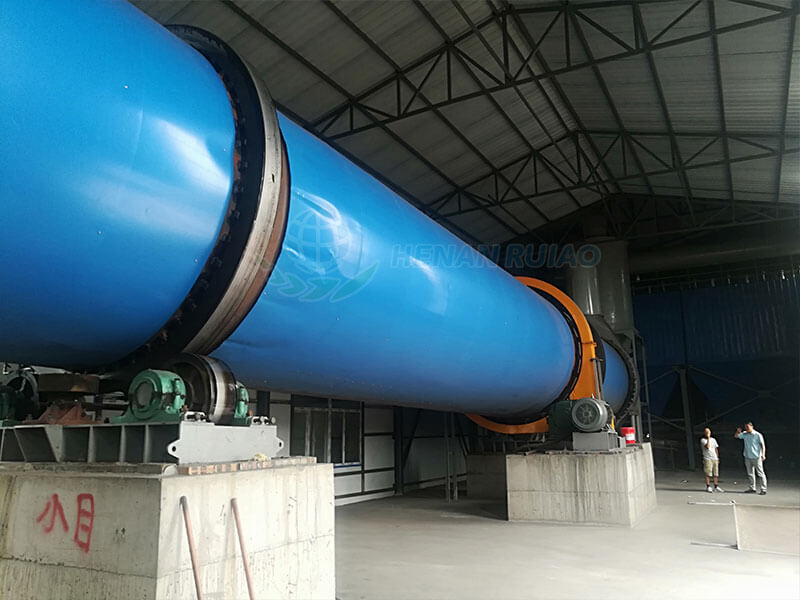
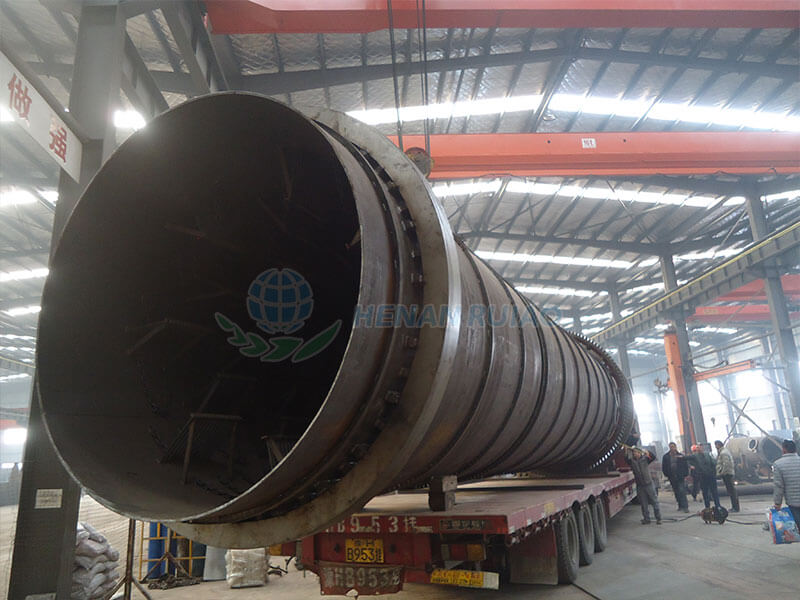
Introduction
The new type of lignite dryer equipment has made qualitative improvements in clean environmental protection and energy-saving and consumption reduction technologies, adapting to the current clean treatment requirements of lignite reprocessing and utilization. Based on the development trend of lignite reprocessing, Henan Ruiao has increased the development of coal drying and quality improvement technology on the basis of deep development of lignite dryer technology.
Features
1. The specially designed lignite crushing and buffering feeding equipment effectively alleviates problems such as uneven, discontinuous, and large instantaneous feeding amount.
2. Continuously improving feeding propulsion equipment, making feeding more uniform and smooth, significantly improving heat resistance and reliability.
3. Fiberglass and stainless steel materials are used in dust removal systems to solve dust removal technical problems such as wear and corrosion.
4. The successful application of bag filter has opened up new ideas for high-temperature and high humidity tail gas dust removal.
5. The advanced, reliable and practical power supply, distribution and control system has greatly improved the automation level of the system.
Composition
The lignite drying system mainly consists of a heat source, dispersed feeding, belt feeding machine, drum equipment, unloader, dust removal equipment, belt discharge machine, induced draft fan, and power distribution operation.
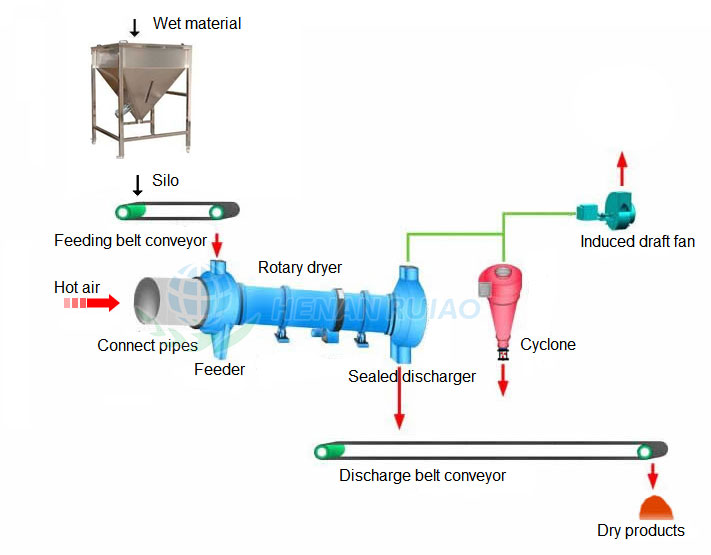
Working Principle
The material is shoveled into the crushing feeder by the loader. Then, it is transferred to the feeding belt conveyor by the dispersing feeder, and then sent to the drum spiral propulsion device by the feeding belt conveyor. Afterwards, it is quickly guided to the inclined lifting area by a large angle guide plate, and with the rotation of the drum and the inclination of the cylinder, it is lifted from the bottom and top of the drum to form a “material curtain”. The high-temperature flue gas that enters the drying drum at the same end as the wet material passes through it, causing the wet material to form conduction and convective heat exchange, preheating the wet material and evaporating some moisture.
Technical Parameters
Model | Capacity(T/D) | Input Moisture(%) | Output Moisture(%) | Power(kw) | Floor Space(㎡) |
RAMG1918 | 300±10 | 25±5 | 13±2 | 109 | 7m×25m |
RAMG2218 | 500±10 | 25±5 | 13±2 | 128 | 8m×30m |
RAMG2520 | 700±12 | 25±5 | 13±2 | 240 | 8m×30m |
RAMG2822 | 1000±15 | 25±5 | 13±2 | 400 | 8m×40m |
RAMG3024 | 1200±20 | 25±5 | 13±2 | 480 | 12m×50m |
RAMG3428 | 1500±30 | 25±5 | 13±2 | 600 | 12m×60m |
RAMG3830 | 1800±30 | 25±5 | 13±2 | 800 | 16m×70m |
RAMG4032 | 2000±30 | 25±5 | 13±2 | 1000 | 18m×70m |
RAMG4238 | 2500±30 | 25±5 | 13±2 | 1200 | 20m×80m |
Send a Message
Get In Touch!
Address
No.11 Changchun Road, High-Tech Development Zone, Zhengzhou, Henan, China
- 19900970386